PhasePot is supporting Rautomead in refining inhouse casting processes and maintaining high-quality grain structure.
Simulated microstructure of VUCC in different casting conditions in comparison with experiments.
High quality Oxygen Free Copper (OFC) products are of a great interest to the automotive and power industries due to their superior performance in electrical conductivity, heat transfer and corrosion resistance. Rautomead has shown the Vertically Upward Continuous Cast (VUCC) process to be an excellent option to cast high quality rods of OFC within a wide range of diameters and exceptional ability for downstream processing. On the other hand, Rautomead also recognises the challenges associated with this process and the need to control and refine certain parameters in order to maintain high quality grain structure while trying to increase casting rate.
Post processing of cast products is generally required to obtain the properties of the end product. To process continuous cast material the castings are often continuously rolled, formed or drawn to final cross-sectional area. This reduction decreases grain size and enhances the mechanical properties. Therefore, it is essential to maintain a homogeneous structure throughout the length of the casting. Inhomogeneities lead to localised mechanical property variances in properties which can lead to failures during processing. These inhomogeneities arise from the repeating periodic withdrawal pattern the cast material undergoes during solidification. The required pattern is material dependant and can vary significantly.
To develop improved production processes and techniques, an accurate prediction of the cast behaviour is required. Traditional approach involves running costly casting trials and evaluating retrospectively the outcome, whilst coupled numerical simulations offer a lower cost alternative to predict the casting outcome, reducing the need for costly trials significantly.
Small pulse
Large pulse
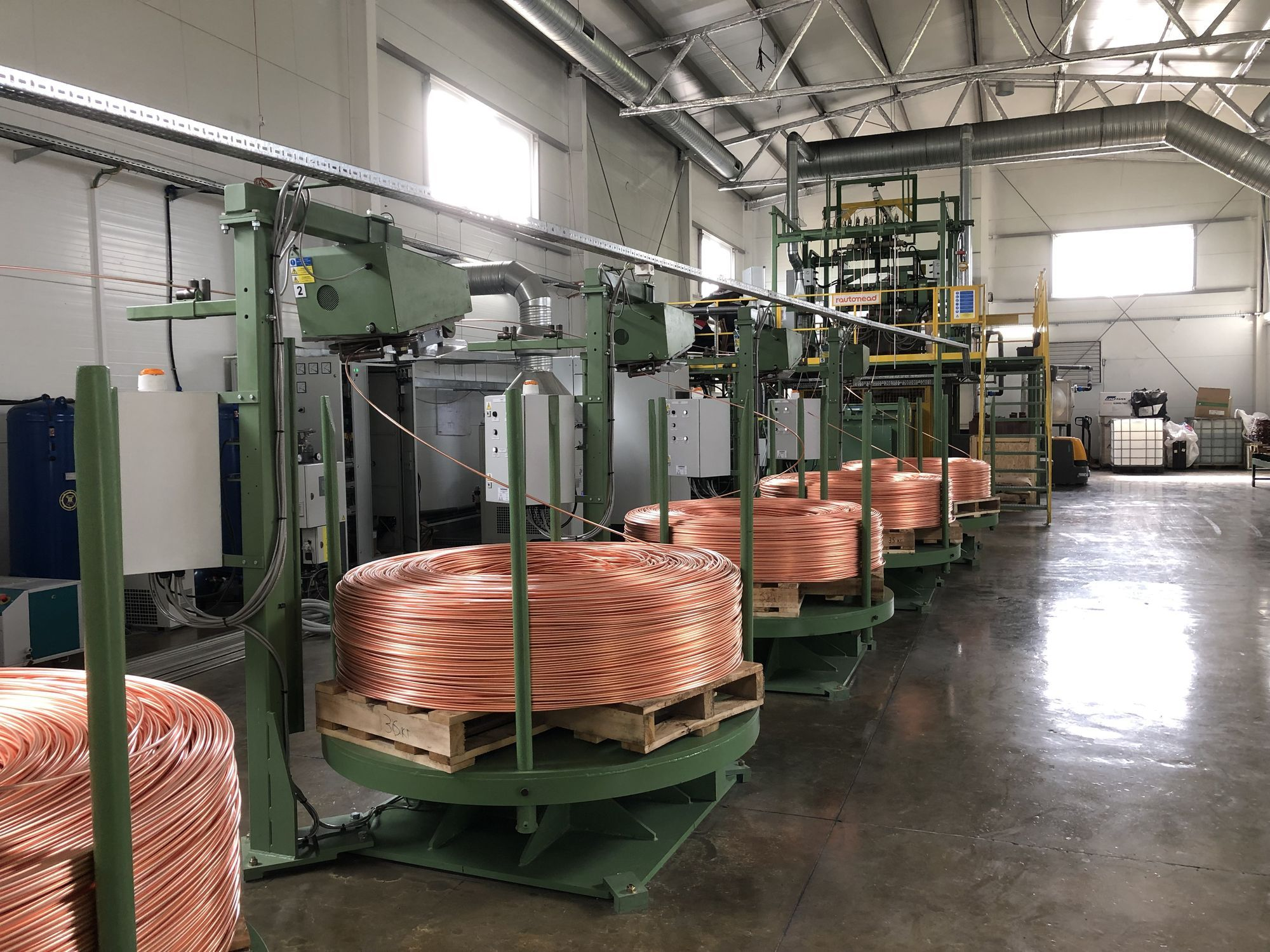
“Thanks to PhasePot’s capabilities and the great support we received from their technical experts over the last few years, we have been able to gain a more comprehensive insight of the grain evolution during the VUCC process. Our Simulation & Modelling enhanced R&D programme is keeping the improvement of our continuous casting technology at the cutting edge while saving a lot of resources by minimising the need for physical trials.”
Brian Frame, Managing Director of Rautomead
PhasePot software was employed to simulate microstructure evolution during VUCC of OFC at different casting speeds and control parameters. The development of combined Phase-field and Monte Carlo-Potts models provided Rautomead with an insight into the factors controlling the grain structure.
The model was initially validated against a few critical experiments and subsequently used to study the interdependence of casting conditions and the grain structure for a number of ‘what-if’ scenarios. These parameter studies accelerated identification of the ideal casting parameters — leading to producing final products with improved mechanical properties beside significant saving in time and resources by reducing the need to run costly physical trials.
About Rautomead:
Rautomead Limited are UK-based specialists in continuous casting of non-ferrous metals and construction of continuous casting equipment for copper, copper alloys, gold, and silver. They use a variety of continuous casting equipment to produce various alloys, precious metals and more. Since it as established in 1978, Rautomead has evolved to become the world's leading and most experienced supplier of continuous casting technology for non-ferrous alloys.
[Ref.] Jones, T., Strachan, R., Mackie, D., Cooper, M., Frame, B., & Vorstius, J. (2021). Phase Field & Monte Carlo Potts Simulation of Grain Growth and Morphology of Vertically Upwards Cast Oxygen Free Copper. Paper presented at 10th European Conference on Continuous Casting, Bari, Italy.